3D printers
High quality 3D printers
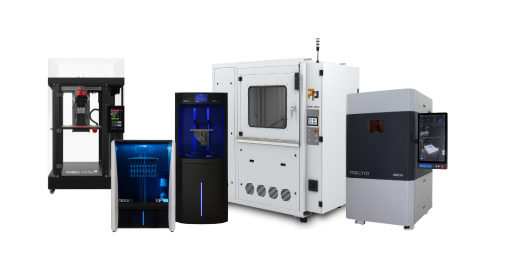
Order high-quality 3D printed parts now at PartsToGo!
3D Print Now!Series production with high quality and quantity
Manufacture high quality metal components
High resolution components in all quantities
High quality components without support structures
Wide range of known materials
Ideal for a variety of indications
For the completion of your components
Production cells enable series production of high volumes
Fast data processing and successful quality management
Sorry, there are no results for this combination of filters. Choose another combination of filters.
To ensure that all requests are handled promptly and completely, we ask that you submit all support requests through our support portal.
To the service portalDo you need assistance with your project, do you need advice or a sample part that we can send you?
Send EmailFill up the form below and we will send you the data sheet by e-mail.
Fill up the form below and we will send you the data sheet by e-mail.
Fill up the form below and we will send you the data sheet by e-mail.
Fill up the form below and we will send you the data sheet by e-mail.
There were a lot of issues with the printers that the Orthodontic Lab Brys-Callewaert had before, like parts that fell off from the Formlabs and the closed structure of the different resin possibilities that made developing new products really expensive. The Stratasys® printers required really expensive resin and were a big cost in maintenance and support. Besides that, the Lab had to scale up the production of parts, which was impossible with a printer that needed 10 hours for one build job.
Fill up the form below and we will send you the data sheet by e-mail.
While additive manufacturing has been at the center of ART’s business since the beginning, today about half of the end products they produce are not 3D printed, but cast urethane. Casting in urethane has allowed ART to produce low cost plastic parts with a quick turnaround. It is a very hands on process that takes a minimum of 24 hours per mold, requires a significant amount of labor, and the end result is a mold capable of up to 25 parts depending on the material being cast. That said, the effort appears worthwhile based on the high demand from their customers. “Our cast urethane is about 50% of our business right now and we’re almost maxed out,” says Bruce LeMaster, Founder and Vice President of ART. In addition to urethane, ART follows a similar 24 hour process for silicone molding. With such high demand, LeMaster and the team at ART were all but maxed out with a very real cap on the volume of projects they could take on.
Fill up the form below and we will send you the data sheet by e-mail.
Keystone Industries, a privately held US company founded in 1908, manufactures thousands of dental products as well as its own KeyPrint line of photopolymer 3D printing resins. While the company already works with nearly two dozen 3D printer partners, Keystone faced the challenge of meeting the high-volume throughputs demanded by busy dental labs. Labs make their money by doing the manufacturing for the doctors. While demand for 3D printed dental products continues to surge, the labs are constrained by the size and throughput limitations of their 3D printers. “The simplest solution would seem to be for a growing lab to simply buy more printers,” notes Keystone 3D printing engineer and lab manager Benjamin Taylor. “But that translates into more expense, more maintenance, and the need for more space. The preferred approach is to use faster, larger-volume 3D printers and to keep them constantly pumping out product.”
Fill up the form below and we will send you the data sheet by e-mail.
The traditional side of the orthodontic lab is a "dusty place", says Tyler Dowdle of Excel Orthodontics. Dentists or orthodontists take impressions or molds, which can be an unpleasant experience for patients. These impressions are sent to the lab with an order for the required device, and the lab manually casts and machines the models, which is time-consuming. However, 3D printers now allow labs to convert intraoral 3D scans into accurate printed models more quickly and with less effort. Excel started transitioning to a digital workflow with their first 3D printer about eight years ago. However, they are now seeking an upgrade because the printers they are currently using come with a high price tag. The manufacturer does not sell their printers but instead leases them for a minimum of $150,000 for three years, after which the customer must return the hardware or start a new lease.
Fill up the form below and we will send you the data sheet by e-mail.
“We receive patient scans from our client offices so we can design an optimal treatment plan for them” explains Cristina Montiel, laboratory technician at Key Dental. “I need to print 20 models per patient” she said, noting that as the business continues to grow quickly, there can be tremendous demands on the practice’s various 3D printers. Speed, throughput and precision are vital. Previous 3D printing solutions offered the accuracy and definition needed for aligner models but lacked the speed and capability of high volume capacity that Key Dental Technologies needed in order to achieve higher throughput critical to their aligner manufacturing.
Fill up the form below and we will send you the data sheet by e-mail.
![]() |
|
Photos from the event |
![]() |
|
|
![]() |
|
|
![]() |
|
On-demand webinar |
![]() |
|
On-demand Webinar |
![]() |
|
Read more |
![]() |
|
Read more |
![]() |
|
Read more |
![]() |
|
Read more |
![]() |
|
Read more |
![]() |
|
Read more |
![]() |
|
Read more |
Cookie settings
We use cookies to provide you with the best possible experience. They also allow us to analyze user behavior in order to constantly improve the website for you. Privacy Policy