3D-Printers
Hoogwaardige 3D-printers
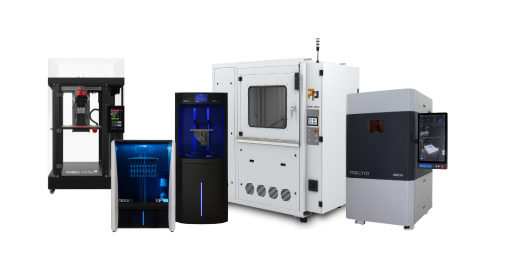
Deze blogpost is een samengevat overzicht van de belangrijkste kenmerken en functionaliteiten van de technologie: 3D-printen met metaal.
Metaal 3D-printen heeft nu vaste voet aan de grond gekregen in de industriële productie. Sommigen glimlachten in het begin enigszins, maar 3D-metaalprinten vervangt nu steeds meer traditionele productiemethoden zoals CNC-frezen, spuitgieten en nog veel meer.
Hieruit kan worden geconcludeerd dat Additive Manufacturing met metaal enkele voordelen moet bieden. Maar ook deze vorm van fabricage techniek is niet immuun voor nadelen. Voordat we ingaan op deze voor- en nadelen, wil ik eerst kort ingaan op de subtypes van deze technologie, hoe deze subtypes werken en de fabrikanten van metalen 3D-printers
Metaal 3D-printen wordt geleverd met meer subtypes dan enige andere technologie binnen Additive Manufacturing. Van "Cold Metal Fusion" tot "Selective Laser Melting", er is veel.
Aangezien er vele sub-technologieën zijn wordt er in deze blog een focus gelegd op de zes belangrijkste van 3D-metaalprinten. De subtypen worden gecategoriseerd onder op ''laser'' gebaseerde en op ''sinter'' gebaseerde printprocessen.
Zoals de naam duidelijk aangeeft werken alle volgende printprocessen met een laser- of elektronenstraal. Met deze laser/elektronenstraal wordt het metaalpoeder verhit en zo versmolten. Daarom zijn er voor dit proces geen externe sinterovens nodig.
Dit type metaal 3D-printen was de eerste manier om metalen componenten te produceren door middel van Additive Manufacturing. Deze mogelijkheid was vooral nodig om de productiesnelheid van complexe metalen onderdelen enorm te verhogen, in tegenstelling tot conventionele productiemethoden.
Deze categorie omvat Selective Laser Melting (SLM), Direct Metal Laser Sintering (DMLS) en Electron Beam Melting (EBM).
Bij Selective Laser Melting wordt een laag metaalpoeder, die zich op een poederbed bevindt, plaatselijk volledig omgesmolten zodat het na stolling een vaste materiaallaag vormt.
De bouwplaat wordt vervolgens met de hoogte van één laagdikte verlaagd en er wordt opnieuw poeder aangebracht. Deze cyclus wordt herhaald totdat alle lagen opnieuw zijn gesmolten.
Het voltooide onderdeel wordt vervolgens vrij gemaakt van poederresten en het support materiaal wordt verwijderd. Dit support materiaal is in dit proces altijd nodig om het metaal in zijn dichtheid en gewicht in de gewenste vorm te houden.
Direct Metal Laser Sintering is qua proces bijna identiek aan Selective Laser Sintering - met één uitzondering. Bij DMLS wordt het metaalpoeder net lang genoeg verhit om moleculaire fusie te laten plaatsvinden, maar niet lang genoeg om te smelten, zoals bij SLM het geval is.
Dit zorgt voor een veel grotere materiaalflexibiliteit, maar tegelijkertijd minder duurzame mechanische eigenschappen dan bij SLM.
Bij Electron Beam Melting, ontwikkeld door het Amerikaanse bedrijf Sciaky, wordt eerst geleidend metaalpoeder in de printer gebracht en vervolgens wordt de interne druk in de bouwkamer verlaagd, waardoor een vacuüm ontstaat. Zodra de ideale interne druk is bereikt, wordt het bouwplatform verwarmd.
Nadat de gewenste temperatuur is bereikt wordt een laag van het metaalpoeder op de bouwplaat aangebracht en een elektronenstraal, die door elektromagnetische spoelen wordt geleid, raakt het poeder op de juiste plaatsen om het te laten stollen.
Het grootste voordeel van EBM ten opzichte van SLM en DMLS is snelheid. De elektronenbundel kan namelijk scheiden om meerdere locaties van het metaalpoeder tegelijkertijd te verwarmen.
EBM biedt echter minder precisie dan de eerder genoemde technologieën. Dit komt omdat de elektronenstraal breder is dan de laserstraal, waardoor de nauwkeurigheid verloren gaat.
Op sinter gebaseerde printprocessen van Additive Manufacturing van metaal zijn een verdere ontwikkeling van productieprocessen die oorspronkelijk zijn ontwikkeld voor polymeer onderdelen. Dit proces wordt gebruikt om groene onderdelen volledig zonder gereedschap te vervaardigen en zo het spuitgieten in enige hoedanigheid te vervangen.
Bij elk van deze processen wordt een mengsel van metaal en polymeer gebruikt voor het printen. Tijdens het printen wordt het polymeer gevormd tot het groene deel en uitgehard, terwijl het metaalpoeder aanvankelijk "onaangeroerd" blijft. Met behulp van een sinteroven wordt het polymeer na het printen volledig thermisch ontleed en wordt het metaalpoeder uitgehard in de door het polymeer gespecificeerde vorm.
Er moet altijd worden opgemerkt dat elk onderdeel kleiner blijkt te zijn dan het groene gedeelte, waarmee natuurlijk rekening moet worden gehouden bij het maken van het digitale model.
Deze categorie omvat Metal Binder Jetting (MBJ), Fused Deposition Modeling (FDM) met metaal en Cold Metal Fusion (CMF).
Bij Metal Binder Jetting wordt het printbed bedekt met een laag metaalpoeder en wordt op de juiste plaatsen een polymeerbindmiddel op de metaalpoederlaag "gespikkeld". Dit bindmiddel wordt uitgehard door de temperatuur in de bouwkamer (ca. 70 °C). Zodra deze uitharding is voltooid, wordt een nieuwe poederlaag aangebracht en wordt het proces herhaald totdat het groene deel is voltooid.
Om mechanische schade te voorkomen, vindt het uithardingsproces meestal plaats terwijl het groene deel in het poederbed is ingebed. Aangezien het poederbed dus permanent als drager voor de groene delen dient, zijn er bij dit type metaal 3D-printen geen extra draagconstructies nodig.
Metal Binder Jetting biedt uitstekende kwaliteit en precisie, maar is een wat langdurig proces. Hoewel het printen relatief snel gaat, moet het groene deel met borstels of perslucht uit het poederbed worden verwijderd en vervolgens in een externe oven worden gesinterd.
Om deze redenen ontplooit MBJ zijn volledige potentieel vooral in de serieproductie van complexe componenten.
Fused Deposition Modeling met metaal werkt vrijwel identiek aan 3D-printen uit filamenten, alleen bestaan de filamenten hier voor een bepaald percentage (meestal 50 - 60%) uit metaalpoeder. Het filament wordt via een spoel door een verwarmde print-extruderkop gevoerd, erin gesmolten en vervolgens laag voor laag op de bouwplaat aangebracht.
Componenten die door dit proces worden geproduceerd, hebben altijd ondersteunende structuren nodig. Deze kunnen echter ook uit een ander materiaal worden gevormd in printers met meerdere extruders, waardoor het verwijderen gemakkelijker wordt.
FDM met metaal biedt een grote gebruiksvriendelijkheid dankzij de eenvoudige bediening en geen poederhantering, evenals lage machine- en materiaalkosten. Kwalitatief is het echter het zwakste proces in het 3D-printen van metaal, zowel qua oppervlaktekwaliteit als qua precisie.
Cold Metal Fusion is het nieuwste van de hier gepresenteerde 3D-printprocessen en is ontwikkeld door Headmade Materials. Bij dit fabricageproces wordt een mengsel van metaalpoeder en bindmiddel, meestal "grondstof" genoemd, puntsgewijs bestraald door lasers om het bindmiddel selectief uit te harden.
Het bouwplatform wordt vervolgens neergelaten en de volgende laag grondstof wordt aangebracht. Dit proces wordt herhaald totdat het groene gedeelte is voltooid. De groene delen worden vervolgens ontdaan van overtollig poeder en gesinterd in een externe oven.
De oplettende lezer zal deze procesbeschrijving al bekend zijn - dit proces lijkt namelijk sterk op Selective Laser Melting. Het grote verschil is de veel lagere energie en kosten die nodig zijn voor het printen, omdat in tegenstelling tot het SLM-proces niet het metaalpoeder zelf wordt uitgehard, maar alleen het bindmiddel.
Er zijn veel verschillende fabrikanten rond het 3D-printen van metaal. Ik zal het hier beperken tot de grootste fabrikanten van professionele en industriële metaal 3D-printers.
Het Amerikaanse bedrijf 3D Systems® maakt naast hun SLA-printers ook 3D-printers voor metaal.
Het metaalportfolio van 3D Systems® bestaat uit de industriële DMP Factory-serie en de professionele DMP Flex-serie.
Desktop Metal® is in 2015 opgericht en is gevestigd in de VS. Ondanks zijn relatief korte bestaan heeft het bedrijf al financiële steun gekregen van onder meer Google en BMW. Desktop Metal® produceert verschillende binderjetting- en FDM-metaal 3D-printers.
De portfolio omvat de X-Series en Production-Series industriële bindmiddelspuitsystemen, evenals de Fiber™, Shop System™ en Studio System™ 2 industriële FDM-metaalsystemen.
Concept Laser is een Duits bedrijf dat nu deel uitmaakt van het Amerikaanse conglomeraat General Electric en zijn dochteronderneming GE Additive. Zij worden beschouwd als een pionier op het gebied van Powder Bed-technologie binnen Additive Manufacturing.
De producten van Concept Laser omvatten de industriële printsystemen X Line 2000R en M Line en de professionele Mlab-serie.
Sciaky is een Amerikaans bedrijf en met de oprichting in 1939 een van de oudste bedrijven rond Additive Manufacturing. Zoals eerder vermeld is Sciaky de ontwikkelaar van het EBM-proces en het enige bedrijf dat printapparatuur produceert met behulp van deze technologie.
Sciaky's portfolio omvat de industriële EBAM 300-, een van de grootste additive manufacturing-systemen ter wereld met een bouwschil van bijna 5,8 meter lang, de EBAM 150- en EBAM 68-serie.
Het Taiwanese bedrijf XYZprinting, dat onlangs grotendeels werd overgenomen door Nexa3D®, produceert industriële metaalpoeder 3D-printers tegen betaalbare prijzen.
Deze industriële metaalpoeder 3D-printers omvatten de MfgPro236 xS (nu QLS236 van Nexa3D®) en MfgPro 230 xS (nu QLS230 van Nexa3D®).
Het in de VS gevestigde Markforged® is opgericht in 2013. Het bedrijf produceert nu naast zijn diverse filament 3D-printers ook enkele metalen 3D-printers.
Deze omvatten het professionele Metal X System™ en het industriële PX100™ printsysteem.
Het grootste voordeel van Additive Manufacturing met metaal is de onbeperkte ontwerpvrijheid in combinatie met de mogelijkheid om zeer complexe componenten te vervaardigen. Van de kleinste details zoals holtes en gaten tot de meest uiteenlopende geometrieën, met metaal 3D-printen zijn er vrijwel geen grenzen.
Een ander groot voordeel is de grote keuze aan materialen. Waar in het verleden roestvrij staal vrijwel het enige beschikbare materiaal was voor het produceren van metalen componenten met behulp van Additive Manufacturing, is er nu een grote verscheidenheid aan metalen met een breed scala aan eigenschappen beschikbaar. Koper, aluminium, titanium, wolfraam en vele andere metalen kunnen nu worden verwerkt door 3D-printsystemen.
Metalen onderdelen zijn vooral nodig in de industrie. Hier komt het volgende voordeel om de hoek kijken: de hoge productievolume. In verreweg de meeste gevallen zijn metalen 3D-printsystemen in staat om veel, soms zelfs verschillende componenten in één keer te printen. Naast de productie van individuele stuks is Additive Manufacturing met metaal daarom ook uitermate geschikt voor serieproductie.
Veel van de Additive Manufacturing-processen voor metaal vereist support materiaal. Dit is normaal gesproken een nadeel omdat ze van het afgewerkte onderdeel moeten worden verwijderd, wat tijd en arbeid kost. Bij 3D-printen met metaal kunnen de ondersteunende structuren echter meestal relatief eenvoudig worden verwijderd met behulp van geschikt gereedschap.
Last but not least wil ik de isotrope microstructuur positief benadrukken. Hierdoor zijn de mechanische en thermische eigenschappen in het gehele onderdeel gelijk, waardoor het gebruik van deze onderdelen ook onder moeilijke omstandigheden geen probleem is.
Natuurlijk gaat ook 3D-printen met metaal niet zonder gebreken.
Een van de grootste nadelen van deze technologie: de kosten. Metalen 3D-printers zijn gemiddeld genomen de duurste Additive Manufacturing-apparatuur. Materiaalkosten zitten ook veelal in het hogere segment. Naast de kosten van printers en materialen kunnen er ook kosten zijn voor sinterovens en andere nabewerkingsapparatuur.
Dit brengt ons ook bij het volgende nadeel: nabewerking. In de overgrote meerderheid van de gevallen moeten componenten van 3D-metaalprinten worden nabewerkt. Of het nu gaat om uitharden, slijpen, verwijderen van support-materiaal of iets dergelijks. Aan het einde van het printen is zelden ook het eindproduct.
Zoals eerder beschreven werken veel van de metaalprinttechnologieën binnen Additive Manufacturing met metaal in poedervorm, waardoor het hanteren van poeder onvermijdelijk is. Dit zorgt er enerzijds voor dat metalen 3D-printers meestal een aparte ruimte nodig hebben zodat het poeder geen andere werkoppervlakken verontreinigt en anderzijds dat industriële veiligheidsapparatuur nodig is voor het gebruik van de printer. Dit zorgt voor extra kosten en vereist geschoold personeel.
Ten slot moet oppervlakteafwerking als nadeel worden genoemd. Hoewel dit op geen enkele manier ondergeschikt is, is het ruwer dan veel andere Additive Manufacturing-processen. Dit maakt metaal 3D-printen ongeschikt voor toepassingen waar zeer gladde of plooibare oppervlakken vereist zijn.
Additive Manufacturing met metaal is nu in veel industrieën een essentiële productiemethode gebleken. Het belangrijkste toepassingsgebied, ongeacht de branche, is de productie van prototypes. Of het nu gaat om de auto-industrie, de ruimtevaart of consumptiegoederen, 3D-printen met metaal maakt snelle en realistische prototypen mogelijk.
Een ander toepassingsgebied voor Additive Manufacturing met metaal is tooling. Het maakt de snelle productie van gereedschappen met een hoge mate van complexiteit mogelijk en de probleemloze vervanging van gereedschappen indien nodig, waardoor de stilstandtijden van productieapparatuur wordt verminderd en de efficiëntie van de productie wordt verhoogd.
Ook medische technologie profiteert van Additive Manufacturing met metaal. Door de meestal kleine hoeveelheden van bijvoorbeeld implantaten, chirurgische hulpmiddelen en gereedschappen en de mogelijkheid om individuele componenten sneller te produceren dan bij enig ander fabricageproces, heeft 3D-printen met metaal nu ook voet aan de grond gekregen op dit gebied.
Last but not least moet de auto-industrie opnieuw worden genoemd als een belangrijk toepassingsgebied - ook buiten prototypes. Of het nu gaat om remklauwen, koelmantels of motoronderdelen, Additive Manufacturing met metaal wordt snel de standaard voor productie binnen de auto-industrie.
Additive Manufacturing van metalen componenten biedt de industrie veel kansen. Goedkopere componenten, gereedschapsloze productie van ''groene onderdelen'' en grotere zelfvoorziening in de productie zijn slechts enkele hiervan. Tegelijkertijd kan echter niet worden ontkend dat er nog enige vooruitgang nodig is voor de wijdverspreide toepassing van deze fabricagetechnologie.
Het positieve nieuws hier is dat deze vooruitgang in snelle stappen steeds dichterbij komt. In het begin zei ik dat additive manufacturing met metaal meer verschillende subtypes heeft dan welke andere Additive Manufacturing-technologie dan ook. Dit is te danken aan het voortdurende onderzoek en de ontwikkeling van dit fabricageproces - juist om het op grotere schaal beschikbaar te maken.
Maar dit onderzoek en deze ontwikkeling maakt deze productietechnologie ook enigszins ondoorzichtig. Er komt zoveel vooruitgang dat het overzicht ervan soms verloren kan gaan.
Wilt u op de hoogte blijven van de laatste ontwikkelingen binnen deze maaktechnologie, dan kan ik u een bezoek aan een showroom of een beurs van harte aanbevelen. Daar kunt u zich door experts laten informeren over veel van deze ontwikkelingen in de branche en hen vragen stellen.
Anders hoop ik dat deze inleiding tot additieve productie van metaal u heeft kunnen helpen een overzicht te krijgen van deze technologie en de mogelijkheden ervan.