3D-Printers
Hoogwaardige 3D-printers
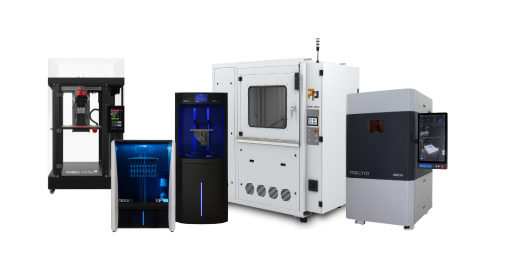
Bestel nu hoogwaardige 3D-geprinte onderdelen bij PartsToGo!
3D-Print nu!De perfecte symbiose van kwaliteit en kwantiteit!
De meest complexe geometrieën met ideale eigenschappen!
Hoogwaardige onderdelen met een grote materiaaldiversiteit!
Krachtige componenten met duurzame productie!
Grote keuze aan materialen en ultrasnelle productie!
Ideaal voor verschillende tandheelkundige indicaties!
Het proces van het simpele onderdeel naar het product!
Volledige automatisering van uw productie!
Snelle verwerking en succesvol management!
Helaas zijn er geen resultaten gevonden voor deze combinatie van filters. Kies voor een andere filtercombinatie.
Om ervoor te zorgen dat alle vragen snel en volledig worden verwerkt, vragen wij u om alle ondersteuningsvragen via ons ondersteuningsportaal in te dienen.
Naar de Support PortalHeeft u ondersteuning nodig bij uw project, heeft u advies nodig of een 3D-geprinte sample nodig die wij u kunnen toesturen?
Email verzendenIn de ogen van veel mensen wordt het woord duurzaamheid vaak geassocieerd met hogere kosten – en helaas is dit voor veel materialen waar.
Bij het recyclen van klassiek plastic, zoals plastic flessen, moeten de verschillende soorten plastic van elkaar worden gescheiden. Ondanks onze inspanningen om verschillende soorten afval te scheiden, belanden veel soorten plastic nog steeds in dezelfde prullenbak. Het plastic moet vervolgens worden gewassen en uiteindelijk opnieuw worden verwerkt. Dit hele proces is kostbaarder dan gewoon nieuw plastic produceren.
De situatie is echter heel anders bij polymeerpoeder in additieve productie. Hier levert het hergebruiken van het materiaal twee voordelen op: het is duurzamer en tegelijkertijd kosteneffectiever dan gewoon nieuw materiaal produceren of kopen.
In deze blogpost zal ik uitleggen hoe het recyclen van polymeerpoeder in 3D-printen precies werkt, welke vereisten er zijn voor probleemloos hergebruik en of er nadelen zijn aan deze recycling.
In de meeste gevallen zijn ondersteuningsstructuren vereist voor elk type additieve productie. Deze zorgen ervoor dat zelfs complexe componenten stabiel blijven tijdens de constructie en niet ineenstorten.
Deze ondersteuningsstructuren moeten natuurlijk worden verwijderd nadat de print is voltooid. Of ze nu met de hand, met een afbraamtool, met schuurpapier of, in het geval van FDM/FFF, met oplosbaar ondersteunend materiaal door middel van wassen, worden verwijderd, de ondersteuningsstructuren zijn na verwijdering bijna uitsluitend productafval.
Bij 3D-printen met polymeerpoeder is dit echter anders. Hier zijn geen klassieke ondersteuningsstructuren nodig, omdat de poedellaag op de bouwplaat zelf voldoende is om het onderdeel te ondersteunen. Dit poeder wordt tijdens het printproces niet gesinterd of gebonden en is daardoor ongebruikt poeder.
Desondanks moet dit ongebruikte of overtollige poeder ook van het onderdeel worden verwijderd. Afhankelijk van de complexiteit van het onderdeel en de uitrusting van de productiefaciliteit, kan dit ofwel met de hand of met machinale ondersteuning, zoals een poederbehandelingsstation, worden gedaan.
Dit overtollige poeder is echter geenszins productafval; het kan worden teruggevoerd naar de printer om verdere componenten te printen. Afhankelijk van de dichtheid en het terugvoersnelheid kan zelfs een volledig printproces worden voltooid met alleen eerder ongebruikt poeder.
De belangrijkste term met betrekking tot het hergebruik van polymeerpoeder is de vernieuwinggraad. Dit is niets anders dan de verhouding van nieuw poeder ten opzichte van gerecycled poeder in een printopdracht.
De vernieuwinggraad varieert afhankelijk van het type polymeerpoeder, de duur van de verwarmings- en koelingscycli van de respectieve printer, de packing density en de toepassingsgebieden van de componenten. Het is erg moeilijk om een exact gemiddelde waarde te geven, maar in de meeste gevallen ligt deze tussen de 20 en 50%. Tegenwoordig zijn er echter ook zogenaamde zero-waste-oplossingen mogelijk, wat betekent dat componenten volledig uit gerecycled poeder kunnen worden gemaakt.
Voordat polymeerpoeder kan worden hergebruikt, moet het echter eerst worden bewerkt. Hoewel het poeder niet wordt geprint, wordt de samenstelling ervan nog steeds beïnvloed door de warmte of de bindmiddelen, vooral in de gebieden direct rond de printopdracht. Dit kan leiden tot klonten tijdens het printproces, wat de kwaliteit van een nieuwe printopdracht negatief zou beïnvloeden.
Deze voorbereiding vindt plaats door het poeder te zeven. Er zijn tegenwoordig een breed scala aan automatiseringsopties voor het zeven, maar handmatig zeven is ook voldoende om het poeder weer volledig functioneel te maken.
De vraag hoe vaak het poeder al is hergebruikt, is ook essentieel voor een ideaal hergebruik. Hoe vaker poeder wordt gerecycled, hoe hoger de vernieuwinggraad en hoe groter de inspanning die nodig is voor het zeven. Het is daarom essentieel om goed in de gaten te houden hoe vaak een poeder al is hergebruikt.
De voordelen van het recyclen van polymeerpoeder zijn in deze blogpost al aangestipt. Van kostenminimalisatie en een snellere return on investment tot het minimaliseren van afval en de bijbehorende milieubescherming, en het verminderen van leveringsrisico’s – de voordelen zijn divers en veelzijdig.
Toch zijn er enkele beperkingen die onvermijdelijk zijn bij het recyclen van polymeerpoeder. Waarschijnlijk de meest ingrijpende beperking is het ruwere oppervlak. Afhankelijk van de vernieuwinggraad en het aantal hergebruik, kan een relatief glad poeder resulteren in een relatief ongelijk eindresultaat.
De term vernieuwinggraad kan ook leiden tot beperkingen. Hoewel veel fabrikanten een ideale vernieuwinggraad specificeren, is een zekere mate van experimenteren essentieel om de ideale componenten voor jouw vereisten te verkrijgen. Experimenteren wordt beloond, omdat je zo de verhouding van nieuw materiaal en de daaruit voortvloeiende kosten precies kunt afstemmen op je eigen behoeften.
Echter, experimenteren brengt een zekere inspanning met zich mee. Hoewel het zeven van oud poeder, het mengen met nieuw poeder en het handhaven van de juiste nieuwe toevoer door automatiseringsopties geen enorme hoeveelheid werk meer met zich meebrengt, gaat er toch tijd verloren.
In principe kan gerecycled poeder voor alle toepassingen worden gebruikt. Mits de vernieuwinggraad juist is, kunnen ook hoogwaardige eindproducten worden geproduceerd met gerecycled poeder. Gerecycled poeder is echter perfect voor prototypes en ontwerpiteraties.
Functionele en geometrische prototypes zijn hierbij bijzonder geschikt. Het mogelijk ruwere oppervlak is voor deze typen prototyping veel minder belangrijk dan bijvoorbeeld voor een ontwerpprototype.
Daarnaast kan hergebruikt poeder ook worden ingezet voor ontwerpiteraties. Dit stelt je in staat om een groot aantal iteraties te produceren met minimale nieuwe kosten. Dit grote aantal iteraties bespaart later ook kosten tijdens de uiteindelijke productie, omdat de intensievere validatie van het eindproduct foutieve ontwerpen of planningsfouten minimaliseert.
De term "zero-waste-oplossing" is al genoemd in deze blogpost. Als deze zero-waste-oplossingen al bestaan, dat wil zeggen dat 100% van het poeder kan worden gerecycled, dan is volledige circulaire productie binnen additieve productie met polymeerpoeders vast en zeker al mogelijk, toch?
Het antwoord op deze vraag is een voorzichtige "ja". Er bestaan al materialen, zoals Bluesint PA12 van Materialise of Windform® XT 2.0 IMG, die zijn gemaakt van 100% gerecycled poeder. Printsystemen, zoals de QLS 260 van Nexa3D®, maken het nu ook mogelijk om hoogwaardige componenten te produceren uit 100% gerecycled poeder, dankzij zeer korte verwarmings- en koelingscycli en een open materiaalplatform.
Waarom dan slechts een voorzichtige ja? Geen enkel polymeerpoeder ter wereld kan namelijk eindeloos worden hergebruikt. Zelfs met korte verwarmings- en koelingscycli zal op een gegeven moment de samenstelling van het poeder zo veel veranderd zijn dat het niet langer kan worden gebruikt voor het produceren van hoogwaardige componenten. Om de hoge kwaliteit te behouden, zal er vroeg of laat nieuw poeder in de cyclus moeten worden geïntroduceerd.
De verscheidenheid aan materialen voor volledig gerecycled poeder is ook nog ver verwijderd van de algemene verscheidenheid aan polymeerpoeders. Bepaalde poeders kunnen nooit volledig worden gerecycled vanwege hun samenstelling. Dit beperkt de keuze en daarmee ook de mogelijke toepassingsgebieden.
Deze beperkingen zouden echter geenszins de vooruitgang van zero-waste-oplossingen moeten verminderen. De mogelijkheid om hoogwaardige componenten over een lange periode te produceren met alleen gerecycled poeder is een enorme stap in de goede richting - zowel qua productiekosten als milieueffect.
En de vooruitgang is beslist nog niet ten einde. Ontelbare bedrijven en fabrikanten van 3D-printers en materialen zijn voortdurend bezig met onderzoek naar hoe het hergebruik van polymeerpoeder nog productiever en efficiënter kan worden gemaakt.
Als je geïnteresseerd bent in het bijhouden van deze ontwikkelingen, blijf dan deze blog in de gaten houden. Zodra er nieuwe baanbrekende vorderingen in dit veld worden gemaakt, kun je er zeker van zijn dat mijn vingers al op de toetsen zullen tikken om het je te laten weten!
Privacy-instellingen
Wij gebruiken cookies om u de best mogelijke ervaring te bieden. Ze stellen ons ook in staat het gebruikersgedrag te analyseren om de website voortdurend voor u te verbeteren. https://production-to-go.nl/privacy tekst: Privacy