3D-Printers
Hoogwaardige 3D-printers
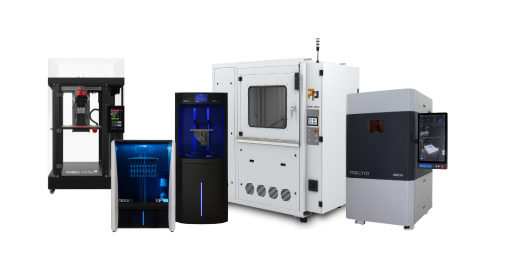
De auto-industrie is altijd een waarborg voor vooruitgang geweest. Of het nu gaat om Henry Ford, die in 1913 de eerste gemecaniseerde assemblagelijn ontwikkelde voor de productie van de Model T en daarmee de auto toegankelijk maakte voor de massa, of om Ôno Taiichi, die in de jaren '50 het "Toyota seisan hôshiki", of het Toyota-productiesysteem, uitvond en zo de basis legde voor het huidige intersectorale systeem van just-in-time productie.
Echter, deze waarborg voor vooruitgang heeft de laatste jaren wat te kampen gehad. De toenemende druk van regelgevers en consumenten op het gebied van energie-efficiëntie, evenals verzwakkende toeleveringsketens, hebben de auto-industrie onder druk gezet om haar productieprocessen opnieuw te revolutioneren - en additieve productie speelt hierin een uitzonderlijk belangrijke rol.
In deze blogpost zullen we eerst kijken naar de geschiedenis van additieve productie binnen de auto-industrie. Vervolgens bekijken we de voordelen die het biedt en tenslotte zullen we enkele toepassingen bekijken waar 3D-printen al traditionele productiemethoden heeft vervangen.
Veel mensen beschouwen 3D-printen als een zeer nieuwe technologie, maar dit is een misvatting. De ontwikkeling van 3D-printprocessen, namelijk de SLA- en SLS-processen, begon al in de vroege jaren '80, en de eerste 3D-printer kwam in 1988 op de markt.
Verschillende autofabrikanten herkenden het potentieel van deze technologie vroeg. In 1988 kocht Ford daadwerkelijk het derde 3D-printingssysteem ter wereld om deze technologie zo snel mogelijk voor zijn doeleinden te valideren. Drie jaar later volgde BMW, en Volkswagen en Porsche in het midden van de jaren '90.
In die tijd werd 3D-printen uitsluitend gebruikt voor rapid prototyping. De snelle productiesnelheden en vereenvoudigde aanpassingen van modellen waren ideaal om de iteratietijden te verkorten en testprocedures intensiever uit te voeren.
Echter, additieve productie was in die tijd nog niet geschikt voor eindgebruikonderdelen. Hoewel 3D-printen destijds al in staat was om de kosten en tijd die nodig waren voor prototypingprocessen aanzienlijk te verlagen, werden veel autofabrikanten afgeschrikt door de hoge aanschafkosten.
De eerste "hype" rond 3D-printsystemen begon uiteindelijk in de vroege jaren 2010. Nieuwe fabrikanten verschenen vrijwel uit het niets, de keuze aan materialen werd aanzienlijk uitgebreid en de ontwikkeling van desktop 3D-printsystemen minimaliseerde ook de aanschafkosten.
Een groot aantal autofabrikanten sprong op de spreekwoordelijke "hype trein". Toyota, Fiat, Kia, Chevrolet, Bugatti en vele anderen richtten zich nu op 3D-printen. Aanvankelijk was dit ook bijna uitsluitend voor prototyping, maar de enorme uitbreiding van het materiaalassortiment opende snel nieuwe toepassingsgebieden voor 3D-geprinte onderdelen - van reserveonderdelen tot "legacy parts" en eindgebruikonderdelen.
Echter, zo'n hype trein blijft zelden lang bestaan. De beste manier om te beoordelen of een product of technologie de hype waard was, is of het in gebruik blijft, zelfs nadat de hype is verdwenen. Heeft 3D-printen de hype in de auto-industrie waar kunnen maken?
Het antwoord was al duidelijk uit mijn voorwoord en is een overtuigend ja. Alleen al in de afgelopen vijf jaar zijn de 3D-printmiddelen bij verschillende autofabrikanten enorm uitgebreid.
In 2020 opende BMW bijvoorbeeld zijn “Additive Manufacturing Campus” in Oberschleissheim, niet ver van München. Hier zijn alleen al ongeveer 50 verschillende 3D-printsystemen in gebruik met als doel additieve serieproductie te perfectioneren. BMW print wereldwijd jaarlijks al meer dan 300.000 componenten van verschillende types, en bij de opening van de AM Campus zei Milan Nedeljković, lid van de Raad van Bestuur van BMW AG, dat additieve productie “al een integraal onderdeel” van het productieproces bij BMW is.
Volkswagen speelt ook nog steeds mee in de topklasse als het gaat om 3D-printen van auto-onderdelen. In 2021 werd bindmiddeljettechnologie geïntegreerd in de hoofdvestiging in Wolfsburg en trainees aan de Volkswagen Academy in Emden worden nu ook intensief opgeleid in het gebruik van 3D-printers - een duidelijk bewijs dat VW 3D-printen als een baanbrekende technologie ziet.
Vanwege tijdsdruk is het natuurlijk niet mogelijk om elke nieuwe ontwikkeling en uitbreiding van 3D-printen in dit blogbericht voor te stellen, maar ik wil een klein vooruitzicht op de toekomst geven. Het gerenommeerde marktonderzoeksinstituut Mordor Intelligence™ schat de jaarlijkse groei van 3D-printen binnen de auto-industrie op 21,74% - van 1,21 miljard dollar naar 3,86 miljard dollar - en toont daarmee de grote groeikansen van 3D-printen in deze sector.
Het feit dat additieve productie zich heeft weten te vestigen in de auto-industrie suggereert dat het een aantal voordelen moet bieden die niet beschikbaar zijn bij conventionele productiemethoden - en dit is precies wat we nu gaan bekijken.
Het eerste voordeel is ook het voordeel dat Ford, en later BMW en Volkswagen, vroege aanhangers van 3D-printen heeft gemaakt. De uitzonderlijk snelle productiesnelheid die mogelijk wordt gemaakt door 3D-printen is essentieel geworden voor prototyping in het bijzonder, maar ook voor de productie van reserveonderdelen.
In prototyping stelt deze verhoogde snelheid ontwerpers en ontwikkelaars in staat om hun ideeën direct in de praktijk te brengen. Hierdoor kunnen ontwerpen sneller worden geoptimaliseerd, eigenschappen sneller worden getest en potentiële fouten sneller worden geëlimineerd. Deze verkorte productietijd zorgt ook voor een grotere veiligheid, aangezien de betreffende ontwerpen intensiever kunnen worden getest.
Wat betreft reserveonderdelen stelt additieve productie het just-in-time-proces in staat om te worden geperfectioneerd. Er zijn geen volgepakte magazijnen nodig als nieuwe componenten in de kortst mogelijke tijd kunnen worden geproduceerd. Dit betekent dat de opslagkosten kunnen worden verlaagd door de verminderde opslagruimte, evenals het opslagrisico.
En natuurlijk is een hoge productiesnelheid nooit een slechte zaak, zelfs niet voor eindgebruikonderdelen. Een snellere tijd naar de markt en een snellere reactietijd op markt- of regelgevingsveranderingen zijn slechts twee van de vele mogelijkheden die 3D-printen biedt voor eindgebruikonderdelen.
Een ander voordeel voor de automobielproductie is de bijna onbeperkte ontwerpvrijheid die 3D-printen biedt. Hierdoor kunnen de meest complexe kenmerken, zoals holtes, slangen- en honingraatstructuren of zelfs de kleinste details, nauwkeurig worden geproduceerd en op elk moment worden gerepliceerd.
Aan de ene kant helpt deze ontwerpvrijheid ontwerpers om hun ideeën zonder beperkingen te realiseren. In combinatie met de snelle printsnelheid en het lage materiaalverbruik van 3D-printen maakt het ook experimenteren met nieuwe vormen en structuren mogelijk die de prestaties of energie-efficiëntie kunnen verhogen.
3D-printen helpt echter niet alleen bij de energie-efficiëntie in de productie zelf, maar ook in de ontwerpfase. Door middel van topologie-optimalisatie, generatief ontwerp en, indien nodig, het gebruik van roosterstructuren kunnen gewichtsoptimalisaties van wel 70% worden bereikt vergeleken met conventionele productiemethoden.
Als gevolg van deze gewichtsoptimalisatie heeft een voertuig natuurlijk minder energie nodig om te bewegen. Dit komt zowel de portemonnee van de gebruiker als het milieu ten goede. Bovendien vermindert deze optimalisatie het materiaalverbruik, wat ook een positieve invloed heeft op kosten en het milieu - en ons ook bij ons volgende grote voordeel brengt.
Lagere emissiewaarden zijn natuurlijk meer dan wenselijk voor motorvoertuigen, maar er is ook een grote drang naar milieubescherming en een circulaire economie als het gaat om productie - en 3D-printen kan aan deze behoefte voldoen.
Terwijl conventionele processen subtractief werken, produceert 3D-printen componenten door ze laag voor laag op te bouwen. Dit betekent dat alleen het materiaal dat nodig is voor het onderdeel wordt gebruikt. Het enige materiaalafval dat door 3D-printen ontstaat, zijn de ondersteuningsstructuren en, in het geval van hars- en poeder 3D-printen, enige overtollig materiaal.
Bijzonder poeder 3D-printen is ideaal om materiaalafval nog verder te minimaliseren. Dit komt omdat het overtollige materiaal, dat ook als ondersteuningsstructuur dient in poeder 3D-printen, gemakkelijk kan worden gerecycled. Je kunt hier een geschikt blogbericht vinden over het proces van recycling van polymeerpoeder.
Al met al biedt 3D-printen de ideale mogelijkheid om de industriële productie milieuvriendelijker te maken en tegelijkertijd kosten te besparen, aangezien verminderd materiaalafval natuurlijk ook leidt tot lagere materiaalkosten.
De perfectie van het just-in-time-proces is al genoemd onder hoge productiesnelheid. Dit geldt echter niet alleen voor 3D-geprinte auto-onderdelen, maar voor het hele productieproces.
Een 3D-printer kan ook ideaal samenwerken met andere productiemethoden om de productie minder afhankelijk te maken van potentiële problemen in de toeleveringsketen, vooral door de mogelijkheid om in-house productiehulpmiddelen met één druk op de knop te vervaardigen.
Of het nu gaat om gereedschappen, steunen, bevestigingen of vormen van alle soorten, van spuitgietvormen tot dieptrekvormen, 3D-printen maakt het mogelijk om deze productiehulpmiddelen individueel aan te passen aan de respectieve toepassing en snel te printen.
Dankzij de zeer brede selectie van materialen is het nu ook mogelijk om alle potentiële noodzakelijke materiaaleigenschappen voor productiehulpmiddelen te vinden - van hittebestendig en vlamvertragend tot flexibel en chemisch bestendig. Hierdoor biedt 3D-printen maximale onafhankelijkheid voor alle processen binnen de autoproductie.
In het laatste deel van deze blogpost wil ik kijken naar enkele van de verschillende toepassingsgebieden voor 3D-printen binnen de auto-industrie. Ik zal eerst de respectieve toepassingen in principe uitleggen en vervolgens een specifiek voorbeeld geven om een gedetailleerder inzicht te bieden in de mogelijkheden van additieve vervaardiging.
Aangezien de voordelen van snel prototyping al in deze blogpost zijn genoemd, zal ik een algemene uitleg achterwege laten en in plaats daarvan twee specifieke voorbeelden geven.
Ten eerste is er Audi, dat nu een verscheidenheid aan verschillende prototypes produceert met behulp van 3D-printen, zoals achterlichtkappen met Stratasys® full-color PolyJet™ printers. Deze full-color mogelijkheid biedt een nieuw niveau van realisme in prototypes, wat het prototypingproces verder kan versnellen.
Een ander zeer spannend voorbeeld komt van bandenfabrikant Michelin®. In 2019 presenteerden zij het eerste prototype van hun nieuwe band genaamd Uptis (Unique Puncture-Proof Tire System). Deze 3D-geprinte prototypeband is volledig luchtloos en vermindert daardoor het risico op lekrijden aanzienlijk. De eerste kilometers werden in 2021 met deze band gereden en de band zou later dit jaar op de markt moeten komen.
In verschillende industrieën willen potentiële klanten steeds meer personalisatie in hun producten, en in veel van deze industrieën wordt 3D-printen al gebruikt om aan deze wens te voldoen - inclusief de auto-industrie.
3D-printen kan deze wens zo efficiënt vervullen omdat de aanpassing van het digitale model eenvoudig en snel kan worden gedaan. In tegenstelling tot veel conventionele productiemethoden is er geen herinstelling nodig - voeg gewoon het gewijzigde model toe aan de printopdracht en ontvang het aangepaste onderdeel enkele uren later.
Een praktisch voorbeeld hiervan wordt gegeven door de sportwagenfabrikant Lamborghini met zijn Sián Roadster. De luchtuitlaten aan de achterkant van het voertuig, die zijn 3D-geprint met een koolstofvezelcomposietmateriaal, kunnen bijvoorbeeld worden gepersonaliseerd met initialen of kleine logo's, waardoor elke Sián Roadster uniek is.
Legacy-onderdelen zijn bepaalde voertuigcomponenten waarvan de productie lange tijd geleden is stopgezet. Wanneer zo'n legacy-onderdeel nodig is, bijvoorbeeld voor reparaties, zijn de acquisitiekosten extreem hoog.
3D-printen kan dit probleem heel eenvoudig oplossen. Alles wat nodig is, is een digitaal model van het betreffende onderdeel of, als er geen digitaal model beschikbaar is, een 3D-scanner om het oude onderdeel om te zetten in een digitaal model. Het legacy-onderdeel kan zelfs worden verbeterd door middel van de eerder genoemde ontwerpoptimalisaties. Duurzaamheid, gewicht, materiaalverbruik en nog veel meer kunnen met het digitale model worden aangepast.
Klein ondernemer Shane Drake uit Maine maakt bijvoorbeeld gebruik van deze voordelen. Hij gebruikt 3D-printers van Raise3D om componenten voor vintage Japanse auto’s te reproduceren. De combinatie van 3D-printers en Shane's ambacht stelt hem in staat om deze legacy-onderdelen optimaal te reproduceren.
Motorcomponenten behoren tot de duurste onderdelen in de auto-industrie. Ze moeten uitzonderlijke duurzaamheid, hittebestendigheid en veerkracht hebben, wat betekent dat alleen hoogwaardige materialen kunnen worden gebruikt en dat deze componenten met extreme precisie moeten worden vervaardigd.
3D-printen kan aan beide eisen voldoen - en tegelijkertijd de kosten verlagen. De eerder genoemde materiaaleconomie speelt hier opnieuw een rol en zorgt ervoor dat autofabrikanten enorme kostenbesparingen kunnen realiseren.
Daarnaast profiteren motorcomponenten ook enorm van de hoge mate van ontwerpvrijheid. Hierdoor is het bijvoorbeeld mogelijk om complexe koelkanalen te produceren die het thermisch beheer verbeteren en zo de efficiëntie en levensduur van motoren verhogen.
Porsche is een van de pioniers op het gebied van 3D-geprinte motorcomponenten. Een voorbeeld hiervan zijn de 3D-geprinte motorzuigers in de Porsche 911 GT2 RS, die niet alleen 10% lichter zijn, maar ook geïntegreerde koelkanalen hebben, wat resulteert in een vermogensverhoging van 30 pk.
Aan het einde van deze blogpost rijst natuurlijk de vraag of er nu volledig of in ieder geval bijna volledig 3D-geprinte auto’s bestaan. We zullen waarschijnlijk nog iets langer moeten wachten op echt volledig 3D-geprinte auto’s, maar er zijn verschillende voertuigen die grotendeels 3D-geprint zijn.
De eerste bijna volledig 3D-geprinte auto werd al in 2014 geproduceerd. De zogenaamde “Strati” werd gepresenteerd door Local Motors in samenwerking met Cincinnati Incorporated en het Oak Ridge National Laboratory op de International Manufacturing Technology Show in Chicago, waarbij het printproces slechts 44 uur duurde. De individuele componenten moesten echter nog gefreesd en over een periode van drie dagen geassembleerd worden. Alleen de batterij, banden en enkele kleinere onderdelen van dit voertuig werden nog met conventionele productiemethoden vervaardigd.
Een ander voorbeeld is de Czinger 21C. Bijna het gehele chassis, de vering en de uitlaatcomponenten van deze hybride sportwagen zijn geproduceerd met additieve vervaardiging. De Czinger 21C werd in 2020 in Londen gepresenteerd, maar er zullen slechts 80 modellen te koop zijn.
Het eerste grotendeels 3D-geprinte voertuig dat massaproductie heeft bereikt, is de XEV Yoyo van de Hong Kong start-up XEV. Dit elektrische stadsvoertuig is volledig 3D-geprint, met uitzondering van de ramen, het chassis en de stoelen. Het voertuig is sinds 2021 in productie en is dankzij zijn concurrerende prijs en slanke ontwerp zeer populair in grote steden.
3D-printen heeft zich de afgelopen jaren duidelijk gevestigd binnen de auto-industrie. Van een prototypingtool is het uitgegroeid tot een garant voor snelle en hoogwaardige productie van een verscheidenheid aan verschillende auto-onderdelen.
Echter, deze ontwikkeling is nog lang niet voorbij. Of het nu gaat om stadsauto's, sportwagens of racewagens - een groot aantal fabrikanten werkt continu aan nieuwe ontwikkelingen en vooruitgangen om de voordelen van additieve vervaardiging voor alle auto-onderdelen beschikbaar te maken.
Als u op de hoogte wilt blijven van de laatste ontwikkelingen in 3D-printen binnen de auto-industrie, controleer dan regelmatig deze blog - want als er nieuwe ontwikkelingen zijn, vindt u ze hier zo snel mogelijk!
Bedankt voor uw aandacht - en tot de volgende blogpost!