3D-Printers
Hoogwaardige 3D-printers
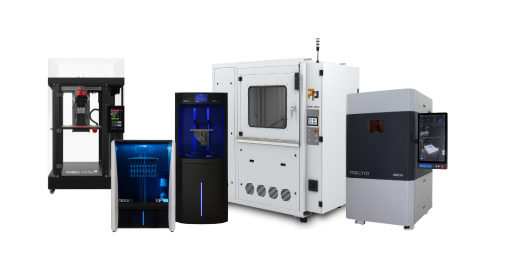
Sinds de ontwikkeling begin jaren 1980 in Japan is geëxpandeerd polypropyleen (EPP) een steunpilaar geworden in veel hoogwaardige industrieën. Of het nu gaat om de auto-, luchtvaart-, bouw- of vele andere industrieën, EPP is nu ongetwijfeld het materiaal bij uitstek voor onderdelen die een uitstekende slagvastheid en energieabsorptie vereisen en tegelijkertijd licht van gewicht zijn.
In het bijzonder heeft EPP zich voor deze hoogwaardige toepassingen weten te handhaven tegenover EPS, expanderend polystyreen, beter bekend onder de handelsnaam Styrofoam®. Dankzij de verbeterde slagvastheid, recyclebaarheid en ontwerpflexibiliteit kan EPP op veel meer gebieden worden gebruikt dan alleen de bovengenoemde. In het bijzonder heeft EPP zich voor deze hoogwaardige toepassingen weten te handhaven tegenover EPS, expanderend polystyreen, beter bekend onder de handelsnaam Styrofoam®. Dankzij zijn verbeterde slagvastheid, recycleerbaarheid en ontwerpflexibiliteit kan EPP steeds meer toepassingsgebieden ontsluiten in vergelijking met EPS, wat wordt ondersteund door de voorspelling van een samengesteld jaarlijks groeipercentage van de EPP-markt van 7,21% tegen 2029.
Traditioneel wordt EPP gevormd met behulp van metalen matrijzen, bijvoorbeeld van gereedschapsstaal of aluminium. Deze conventionele mallen hebben echter een aantal nadelen die de kosten en productietijd verhogen.
Inmiddels biedt filament 3D printen, ook bekend als FDM of FFF 3D printen, de mogelijkheid om deze nadelen te overwinnen. In deze blogpost wil ik het proces van EPP mallen maken introduceren, de voordelen van 3D printen voor het maken van mallen bespreken en de ideale materialen en printapparatuur voor dit proces laten zien.
EPP wordt geleverd in de vorm van zeer kleine bolletjes, die eerst een paar uur worden 'voorgeëxpandeerd' in een stoomkamer of met een blaasmiddel, waarna de nu iets grotere bolletjes 12 tot 48 uur kunnen rusten. Dit proces bepaalt de celstructuur van de bolletjes en geeft EPP zijn karakteristieke eigenschappen.
In de volgende stap wordt de mal gebruikt. Deze bestaat uit twee matrijshelften, een mannelijke en een vrouwelijke, met een holte die overeenkomt met de vorm van het eindproduct. De EPP parels worden nu in deze malholte geplaatst en er wordt klemkracht uitgeoefend op de twee malhelften om ze gelijkmatig bij elkaar te houden.
Vervolgens wordt stoom met een temperatuur tussen 100 en 150 °C in de malholte gebracht. Deze stoom verzacht niet alleen het oppervlak van de parels, maar vergemakkelijkt ook de verdere uitzetting van het materiaal.
Om ervoor te zorgen dat de stoom gelijkmatig wordt verdeeld in de mal en dat de toevoer van lucht en de afvoer van stoom worden gecontroleerd, zijn de mallen op bepaalde punten voorzien van poreuze structuren om een ideale circulatie te garanderen.
Na enige tijd onder invloed van stoom zijn de oppervlakken van de parels zo zacht dat ze samensmelten met de oppervlakken van de omringende parels. Dit resulteert in een continue, monolithische schuimstructuur, terwijl het materiaal tegelijkertijd blijft uitzetten, terwijl de celstructuur van het materiaal en dus de karakteristieke eigenschappen behouden blijven.
Zodra het EPP is uitgehard in de door de holte bepaalde vorm, wordt de klemkracht gedurende korte tijd op de twee malhelften gehandhaafd terwijl het schuim langzaam afkoelt. Zodra het volledig is afgekoeld, wordt de klemkracht verwijderd en wordt het afgewerkte deel uit de twee matrijshelften gehaald. Het gietproces zelf, exclusief de koeltijd, duurt slechts een paar minuten.
Indien nodig kan het schuim nu worden afgewerkt met verschillende nabewerkingsmethoden. Van op maat snijden en oppervlaktebehandeling tot kleuren - de mogelijkheden voor nabewerking zijn bijna eindeloos.
De focus ligt natuurlijk op de matrijs in het EPP vormproces, ook wel stoomkamer genoemd. 3D-printen is bij uitstek geschikt voor de productie van deze matrijzen, omdat het veel van de knelpunten oplost die gepaard gaan met metaalproductie.
Ten eerste, een van de belangrijkste aandachtspunten voor elke productie - kosten. Aangezien de EPP mal speciale eigenschappen vereist, zoals een hoge hittebestendigheid, zijn alleen speciale hoogwaardige materialen geschikt voor 3D printen. De materiaalkosten alleen al zijn in eerste instantie hoger dan voor traditionele metalen halffabrikaten - dit kostennadeel wordt echter niet alleen gecompenseerd door de verwerkingskosten, maar meer dan gecompenseerd, wat resulteert in een aanzienlijke totale verlaging van de totale productiekosten van gemiddeld 40%.
Dit komt voornamelijk doordat de poreuze structuren die nodig zijn in de matrijs niet tegen hoge kosten gefreesd of gelaserd hoeven te worden, maar gewoon in het ontwerp van het digitale model geïntegreerd kunnen worden, waardoor de 3D-printer de afgewerkte matrijs direct met de poreuze structuur kan printen. Met de juiste software kan de structuur zelfs nauwkeurig worden aangepast om de oppervlaktedichtheid van het latere EPP-onderdeel te veranderen. Bovendien voorkomt de directe integratie van deze poreuze structuren materiaalverspilling, wat zowel kosten als het milieu spaart.
Een andere belangrijke factor voor elke productie is tijd - en ook hier kunnen 3D-geprinte EPP matrijzen hun traditionele tegenhangers overtreffen. Omdat de mallen sterk in grootte kunnen verschillen, is het moeilijk om een exacte vergelijking te maken, maar gemiddeld kan 3D-printen ongeveer 60% aan productietijd besparen.
Maar 3D geprinte matrijzen besparen niet alleen tijd in productietijd, maar ook in het vormproces. Omdat de materialen die geschikt zijn voor deze toepassing allemaal uitstekende isolerende eigenschappen hebben, gaat er geen warmte verloren tijdens het gietproces, wat de cyclustijd met wel 34% kan verkorten. Bovendien is er veel minder stoom nodig, ongeveer 65%, wat de kosten opnieuw drukt.
Het laatste grote voordeel van 3D-geprinte mallen is de textuurkwaliteit van het EPP-onderdeel. Ondanks het samensmelten van de individuele EPP-korrels heeft het uiteindelijke onderdeel nog steeds een 'korrelachtige' oppervlaktestructuur - iedereen die ooit piepschuim® in zijn handen heeft gehad, is bekend met deze structuur. Hoewel deze structuur irrelevant is voor toepassingen zoals verpakkingsmateriaal, zijn er veel toepassingen waarbij het schuimoppervlak er aantrekkelijker uit moet zien, wat met conventionele mallen alleen kan worden bereikt door nabewerking.
Met 3D-printen kunnen de mallen echter direct worden bedrukt met een textuur die tijdens het vormproces op het EPP-onderdeel wordt overgebracht. Bovendien kunnen kleine kenmerken, zoals belettering of logo's, met veel detail en weinig moeite in het digitale model worden geïntegreerd, zodat ze ook direct op het schuim kunnen worden overgebracht.
Nu we de vele voordelen van additive manufacturing voor EPP matrijzen hebben besproken, moeten we natuurlijk ook de keerzijde belichten - er zouden immers geen voordelen zijn zonder ten minste één nadeel.
Dit ene nadeel van 3D-geprinte EPP matrijzen is hun levensduur, die korter is dan die van conventionele metalen matrijzen. Natuurlijk hangt de exacte levensduur af van de procesomstandigheden, maar gemiddeld kan een mal gebruikt worden om minstens 2000 onderdelen te maken voordat de mal de kwaliteit van het EPP-onderdeel begint aan te tasten.
Dit aantal kan echter worden verhoogd met een paar proceswijzigingen. Aan de ene kant moet het voordeel van minder stoom juist worden benut, omdat een hogere stoomconcentratie de matrijs na verloop van tijd beschadigt. Anderzijds moet de klemkracht zo laag mogelijk worden gehouden om het onderdeel niet onnodig te belasten.
Als deze punten in acht worden genomen, kan het aantal EPP-onderdelen dat met één matrijs wordt geproduceerd oplopen tot meer dan 5000. Dit aantal blijft nog steeds achter bij dat van metalen matrijzen, dat kan oplopen van 10.000 met aluminium tot 1.000.000 met gereedschapsstaal - hoewel de materiaal- en productiekosten voor gereedschapsstaal natuurlijk nog hoger zijn dan voor aluminium.
Daarom is 3D-printen, ondanks de vele voordelen, niet geschikt voor zeer grote volumes. Maar voor industrieën die vaak kleine tot middelgrote series produceren of waarbij de matrijs vaak moet worden aangepast, is 3D printen des te idealer.
Zoals eerder vermeld, vereisen de gebruikte materialen speciale eigenschappen, waaronder hoge hittebestendigheid, een lage uitzettingscoëfficiënt en uitstekende corrosiebestendigheid. Biocompatibiliteit kan ook een voordeel zijn als het schuim later in contact zou kunnen komen met medicatie of voedsel. Dit elimineert natuurlijk meteen standaardmaterialen zoals PLA of ABS uit het selectieproces.
Onze voorkeursopties voor het vervaardigen van EPP-mallen zijn composietmaterialen, zoals Nylon12CF van Stratasys® of PEI, beter bekend onder de merknaam ULTEM™.
We gebruiken specifiek ULTEM™ 1010 als ons werkpaard voor 3D-geprinte EPP-mallen. Met een hitteafwijkings-temperatuur van 214 °C, uitstekende corrosiebestendigheid, biocompatibiliteit en treksterkte is dit materiaal bij uitstek geschikt voor de additive manufacturing van EPP-mallen.
Aangezien dit materiaal een hoge verwerkings-temperatuur vereist, zijn sterk geïndustrialiseerde systemen nodig om het nauwkeurig te verwerken. Onze keuze is de F900™ van Stratasys®.
Dit printsysteem maakt niet alleen indruk door zijn vermogen om ULTEM™ 1010 met gemak te verwerken, maar ook door zijn leidende precisie en herhaalbaarheid, evenals zijn vermogen om bijna isotropische componenten te produceren. Dit zorgt voor een maximale levensduur van de mallen en een gemakkelijke reproductie.
Additive manufacturing is echt geen nieuwe technologie meer. Sinds de conceptie ervan in de jaren 1980 worden echter voortdurend nieuwe industrieën en toepassingsgebieden geopend – en dit geldt nu ook voor de productie van EPP-mallen, wat voornamelijk mogelijk is gemaakt door vooruitgangen in materiaaleigenschappen.
Deze nog relatief jonge toepassing heeft al een grote impact gehad. Verschillende grote schuimproducenten hebben 3D-printen al omarmd, en ik hoop dat deze blogpost zal bijdragen aan het verder vestigen van de voordelen van additive manufacturing in deze industrie.
Als je verdere vragen hebt over deze toepassing, neem dan gerust contact op met onze experts. Wij helpen je graag de juiste oplossing te vinden voor het integreren van additive manufacturing in jouw productie – of dat nu direct met je eigen systeem is of door te produceren als dienstverlener.
Bedankt voor het lezen – en tot de volgende blogpost!