3D-Printers
Hoogwaardige 3D-printers
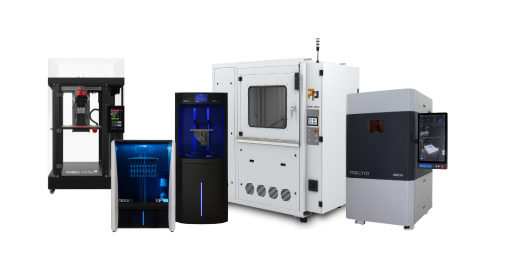
De 3D-printing van metalen componenten wordt steeds gebruikelijker in verschillende takken van de industrie. Of het nu gaat om de automotive sector, gereedschapsfabrikanten, de luchtvaartindustrie of zelfs de medische technologie - de toepassingsgebieden voor additieve productie van metalen componenten worden steeds diverser. Hier kun je een gedetailleerder inzicht krijgen in de voordelen en toepassingsgebieden van metalen 3D-printing.
Echter, de beslissingen rondom additieve productie met metaal worden ook steeds diverser - en daardoor moeilijker. Er komen steeds meer printers, technologieën, fabrikanten en materialen op de markt, wat leidt tot meer gepersonaliseerde opties, maar ook tot langere besluitvormingsprocessen.
Een beslissing die vóór de opkomst van additieve productie al zeer divers was, betreft echter de oppervlakteafwerking van metalen componenten. Al in de jaren '70 waren er talloze processen beschikbaar voor het afwerken van metalen componenten - en additieve productie heeft hier nog meer aan toegevoegd.
De blogpost van vandaag gaat over precies deze talloze processen. Natuurlijk moet ik me in deze blog beperken tot de belangrijkste technieken, aangezien noch ik als schrijver, noch jij als lezer een oneindige hoeveelheid tijd beschikbaar hebt. Deze processen zullen echter hieronder in detail worden behandeld, met hun voordelen en nadelen.
Laten we deze blog beginnen met enkele klassieke technieken voor het afwerken van metalen oppervlakken die lang vóór additieve productie bestonden, maar die ook eenvoudig kunnen worden gebruikt voor het afwerken van metalen componenten die hiermee zijn geproduceerd.
De klassieke methode voor de optische oppervlakteafwerking van metalen is handmatig polijsten. Dit kan gedaan worden op het voltooide, dat wil zeggen al gesinterde, component, maar ook voorafgaand aan de afwerking, terwijl het component zich nog in de groene staat bevindt.
Het grootste voordeel van beide versies is duidelijk de lage kosten. Er zijn geen machines of andere apparatuur nodig, die mogelijk tegen hoge kosten moeten worden aangeschaft, maar alleen schuurpapier of een handpad, tijd en energie.
De resultaten voor componenten met eenvoudige geometrieën zijn ook indrukwekkend na het schuren, vooral als het groene onderdeel al is geschuurd - tot vijf keer fijnere oppervlakken zijn mogelijk dan zonder schuren. Bij deze vorm van schuren moet echter voorzichtig met de kracht worden omgegaan, omdat het component alleen bij elkaar wordt gehouden door de polymeren bindmiddelen.
Het grootste nadeel van deze oppervlakteafwerkingsvariant is voor de hand liggend - de benodigde inspanning. Zelfs het schuren van een kleiner component kan behoorlijk wat tijd in beslag nemen.
Uniformiteit kan ook problemen opleveren bij klassiek schuren. Hoe complexer de geometrieën worden, des te moeilijker het is om een uniforme afwerking te bereiken met handmatig schuren.
Boven een bepaald niveau van complexiteit is handmatig schuren zelfs niet meer mogelijk. Een schuurmachine, hoe goed ook, zal niet ver komen, vooral niet bij interne structuren of de fijnste details.
Desondanks heeft het schuren van componenten duidelijk nog steeds zijn plaats in de wereld van oppervlakteafwerking. Voor zeer kleine bedrijven, met weinig componenten en zeer eenvoudige geometrieën, zijn de aanschafkosten van apparatuur specifiek voor de oppervlakteafwerking van metalen componenten vaak minder aantrekkelijk, waardoor ouderwets handwerk in de toekomst nog steeds de moeite waard zal zijn.
Galvaniseren is het oudste chemische oppervlakteafwerkingsproces dat vandaag de dag nog steeds wordt gebruikt om metalen componenten visueel en functioneel te modificeren. Ontwikkeld in Italië aan het einde van de 18e en het begin van de 19e eeuw, zorgde de relatief geringe toxiciteit van het proces bij het aanbrengen van metalen coatings ervoor dat het procedures verving die eerder kwik gebruikten, zoals vuurvergulden. Sindsdien is het een onmisbaar onderdeel geworden voor veel metaalbewerkende bedrijven.
Bij dit proces wordt gelijkstroom door een elektrolytisch bad geleid met een metaal aan de anode. Dit wordt stukje bij beetje afgebroken door de chemische reactie, waarna de positief geladen metaalionen naar het werkstuk bewegen, dat via een elektrische verbinding de kathode wordt, en zich op het werkstuk afzetten.
De voordelen van dit proces zijn talrijk, maar het belangrijkste is de grote verscheidenheid die galvaniseren biedt. Een breed scala aan materialen kan worden gegalvaniseerd, van goud tot zink, en deze geven natuurlijk hun eigenschappen door aan het component door afzetting op het component. Hierdoor zijn er praktisch geen grenzen aan de kenmerken van 3D-geprinte metalen componenten.
Een ander voordeel is de uitstekende corrosiebescherming die door galvaniseren wordt bereikt. Galvaniseren maakt componenten altijd duurzamer en resistenter, wat vooral belangrijk is voor toepassingen met hoge krachten.
Natuurlijk zijn er ook nadelen aan dit proces. Aan de ene kant is de laagdikte die door galvaniseren wordt bereikt zelden echt uniform. Als uniformiteit vereist is, moet een verder proces, bijvoorbeeld het eerder beschreven schuren, ook worden toegepast.
Een ander nadeel is het gebruik van een groot aantal chemicaliën. Hoewel de lagere toxiciteit van dit proces in vergelijking met zelfs oudere processen enkele alinea’s eerder werd genoemd, worden er toch giftige dampen uitgestoten. Dit betekent dat speciale veiligheidsmaatregelen vereist zijn om dit proces te gebruiken, waardoor het meestal niet geschikt is voor kleine bedrijven.
Vanwege de hoge mate van automatisering is galvaniseren bijzonder geschikt voor bedrijven die grotere hoeveelheden of grotere componenten produceren. Vanwege bepaalde eigenschappen die galvaniseren altijd met zich meebrengt, zoals een verbetering van de corrosieweerstand, is galvaniseren essentieel voor bepaalde industrieën, zoals de luchtvaart, om de geproduceerde onderdelen nog efficiënter te maken.
Stralen is een ander klassiek oppervlakteafwerkingsproces dat zowel de visuele als functionele eigenschappen van een metalen component kan veranderen. De Amerikaanse uitvinder Benjamin Chew Tilghman diende in 1870 een patent in voor het stralenproces, dat in de daaropvolgende decennia verder verfijnd en uitgebreid werd naar een verscheidenheid aan materialen, waaronder metalen.
Hoewel traditioneel zand werd gebruikt, dat met perslucht op het betreffende component werd geblazen, is er nu een breed scala aan verschillende straalmaterialen beschikbaar. Van glas- en keramische bolletjes, slakken en korund tot glas- en notenschalengranulaat - de lijst van mogelijke straalmaterialen kan nog geruime tijd doorgaan.
Deze verscheidenheid aan straalmaterialen leidt ons ook naar het eerste grote voordeel van stralen. Elk straalmateriaal biedt verschillende eigenschappen voor het component. Zo kunnen ruwere oppervlakken worden bereikt met korund of granaatzand, terwijl gladdere oppervlakken kunnen worden verkregen door glasbolletjes of notenschalengranulaat te gebruiken.
Een ander voordeel zijn de relatief lage aankoop- en materiaalkosten. Een mobiele straaleenheid kan al voor een paar honderd euro worden aangeschaft, en een luchtstraalcabine al voor duizend euro. De straalmaterialen kunnen ook zeer goedkoop zijn, bijvoorbeeld slakken of granaatzand.
Een nadeel is de hoge hoeveelheid stof die tijdens het stralen ontstaat. Enerzijds betekent dit dat persoonlijke beschermingsmiddelen (PBM) moeten worden gedragen bij het gebruik van open persluchtstraalmachines, en anderzijds moet al het stof natuurlijk op de een of andere manier worden verwijderd, wat veel tijd kan kosten.
Het is ook belangrijk op te merken dat het oppervlak van het gestralde component heet wordt. Voor de overgrote meerderheid van additief vervaardigde metalen componenten is deze hitte geen probleem, maar voor componenten met zeer dunne wanden kan dit toch tot complicaties leiden.
Vanwege de hoge kwaliteit die stralen oplevert en de lage kosten, heeft deze afwerkingstechniek zich gevestigd als een absolute alleskunner voor veel kleine en middelgrote bedrijven. Vooral wanneer in een bedrijf verschillende materialen worden gebruikt, is stralen ongetwijfeld de moeite waard vanwege zijn veelzijdigheid.
Vibrerende afwerking, ook wel vibrerend schuren genoemd, is het laatste van de klassieke afwerkingsprocessen dat we vandaag zullen bekijken.
Bij dit proces wordt het metalen component in een container geplaatst samen met het schuurmiddel en een vloeibare toevoeging, waarna de container gaat oscilleren of draaien. Dit resulteert in een relatieve beweging tussen het werkstuk en het schuurmiddel, waarbij het oppervlak van het component meestal wordt geschuurd, of minder vaak wordt gepolijst of geslepen.
Een voordeel dat vibrerende afwerking gemeen heeft met stralen, is dat er verschillende schuurmiddelen beschikbaar zijn voor verschillende doeleinden. Deze kunnen gemaakt zijn van keramiek, plastic, natuurlijke producten en meer, en bieden verschillende eigenschappen om het component idealiter af te stemmen op de specifieke vereisten.
Echter, in tegenstelling tot stralen, is er bij dit proces zeer weinig menselijke interactie betrokken. Zodra de vereiste materialen in de container zijn gegoten en de machine is ingeschakeld, is het proces volledig geautomatiseerd en hoeft u alleen maar te wachten totdat het component gereed is en het uit de container te verwijderen.
Deze hoge mate van automatisering betekent echter dat vibrerende afwerkingsmachines allesbehalve goedkoop zijn in aanschaf. De prijzen beginnen bij enkele tienduizenden euro’s, maar kunnen snel boven de honderdduizend euro uitkomen voor grotere machines.
Ondanks de fundamenteel hoge kwaliteit en grondigheid van de oppervlaktebehandeling bij vibrerende afwerking, is dit proces ook niet geschikt voor zeer complexe componenten. Dit proces is ook niet ideaal voor fijne details, omdat het meestal het oppervlak te ruw behandelt voor deze toepassingen.
Vibrerende afwerking is ideaal voor bedrijven die een groot aantal kleinere, eenvoudigere metalen componenten produceren en deze snel willen nabewerken zonder te veel tijd te verliezen. Hoe hoger de productiecapaciteit, hoe sneller de return on investment wordt bereikt dankzij de tijdsbesparing.
Na enkele klassiekers komen we nu bij de processen die specifiek zijn ontworpen voor de oppervlakteafwerking van 3D-geprinte metalen componenten. Aangezien deze processen nog relatief nieuw zijn en de selectie daardoor kleiner is dan bij de klassieke processen, zullen we ons beperken tot de drie belangrijkste technologieën.
In 2016 werd de DryLyte®-technologie gelanceerd door het Spaanse bedrijf GPAINNOVA en dit is het eerste droge elektropolijstproces ter wereld.
Classic elektropolijsten werkt op de tegenovergestelde manier van galvaniseren, dat wil zeggen dat een werkstuk de anode vormt en de combinatie van gelijkstroom en een elektrolytisch bad stukjes van het component verwijdert, waardoor het gladder wordt. De DryLyte®-technologie vervangt het elektrolytische bad door vaste elektrolytp Deeltjes in bolvorm, wat verschillende voordelen heeft.
Een van deze voordelen is dat de DryLyte®-technologie niet alleen de metalen componenten gladder maakt, maar ze ook tegelijkertijd polijst. Vooral in het geval van demonstratiemodellen, waar een glanzend oppervlak van het grootste belang kan zijn, kan dit een aparte en tijdrovende stap volledig elimineren.
Een ander belangrijk voordeel is het zeer lage niveau van toxiciteit dat gepaard gaat met dit type elektropolijsten. De elektrolytp Deeltjes hebben een zeer lage zuurconcentratie, waardoor opslag, hantering en verwijdering mogelijk zijn zonder extra veiligheidsmaatregelen - in schril contrast met klassiek elektropolijsten of galvaniseren.
Echter, de bovengemiddelde lengte van de procesketen moet als nadeel worden genoemd. De componenten kunnen niet zomaar direct van de printer in het polijstproces gaan, maar moeten eerst worden gereinigd en ontvet, en er moet ook schoonmaakwerk worden verricht na het proces om het component volledig bruikbaar te maken.
Bovendien is de reductie van ruwheid tijdens het elektropolijsten beperkt tot een bepaald niveau. Hoewel de DryLyte®-technologie beter presteert dan klassiek elektropolijsten, is het nog steeds inferieur aan andere technologieën zoals stralen of vibrerende afwerking.
Bedrijven die een groot aantal kleine componenten met lage tot gemiddelde complexiteit produceren, profiteren het meest van de DryLyte®-technologie. Vanwege de tijdsbesparing door het gelijktijdig schuren en polijsten, kan ook rapid prototyping aanzienlijke voordelen ondervinden van deze technologie.
De technologie van de Gespannen Rotatiekracht (SRF) werd in 2019 op de markt gebracht door het Amerikaanse bedrijf PostProcess Technologies® en is gebaseerd op het klassieke verwijderingsproces van vibrerende afwerking.
SRF-technologie combineert deze technologie met het gebruik van schuurmiddelen die speciaal zijn ontwikkeld voor additieve vervaardiging. SRF werkt ook met software die de uniformiteit van de mechanische kracht in de container verhoogt.
De voordelen van deze technologie hebben voornamelijk betrekking op de nauwkeurige aanpassing aan additieve vervaardiging. PostProcess Technologies® neemt een al gecertificeerd proces en past het nog nauwkeuriger aan de vereisten van additieve vervaardiging aan – bijvoorbeeld door middel van de eerder genoemde schuurmiddelen.
Dankzij de softwareondersteuning en de verhoogde uniformiteit van de mechanische kracht kunnen zelfs metalen componenten met zeer fijne details voorzichtig worden afgewerkt, wat betekent dat de toepassingsgebieden voor deze technologie verder gaan dan die van klassieke vibrerende afwerking.
Net als bij vibrerende afwerking zijn de acquisitiekosten een van de grootste nadelen. Hoewel de prijs van de machine met SRF-technologie, de zogenaamde RADOR™, zich in het middensegment bevindt vergeleken met andere vibrerende afwerkingsmachines, is het nog steeds duurder dan veel andere oppervlakteafwerkingsmachines.
Een ander nadeel is dat het afhankelijk is van PostProcess Technologies® als het gaat om verbruiksmaterialen. Hoewel PostProcess Technologies® inmiddels een breed scala aan verschillende schuurmedia aanbiedt, kan het zijn dat er geen geschikt schuurmiddel beschikbaar is als je zeer specifieke eisen hebt.
SRF-technologie excelleert in de massaproductie en seriewerk van metalen componenten. In tegenstelling tot vibrerende afwerking kan het ook fijne details verfijnen en is het daarom ideaal voor een breed scala aan industriële toepassingen. Bovendien kan SRF-technologie ook worden gebruikt om 3D-geprinte componenten met andere technologieën, zoals FFF, SLA, MJF en vele anderen, af te werken.
Ons nieuwste proces voor de oppervlakteafwerking van 3D-geprinte metalen componenten komt opnieuw van PostProcess Technologies®. Thermal Atomized Fusillade, of TAF in het kort, werd in 2022 gepresenteerd in de vorm van de DECI Duo™-oppervlakteafwerkingsmachine en is, in tegenstelling tot SRF, geen klassiek proces, maar een volledig eigen technologie.
Deze technologie werkt met twee verticale en één horizontale straalstroom, die een mengsel van perslucht, reinigingsmiddel en zwevende deeltjes in snelle stoten op het component uitstralen. Het component wordt op een draaitafel geplaatst, zodat de uniaxiale straalstromen het gehele component kunnen verwerken.
Het grootste voordeel van deze nieuwe technologie is dat het zelfs de meest complexe componenten kan afwerken. Kleine details, honingraatstructuren en zelfs interne kanalen kunnen met deze technologie worden verwerkt - en dat volledig automatisch.
Een ander voordeel is dat deze technologie niet alleen oppervlakken verfijnt, maar ook ondersteuningsstructuren kan verwijderen. Dit proces is ook zeer veelzijdig wat betreft technologieën. Hoewel het specifiek voor metalen componenten is ontwikkeld, kan het ook FFF-, PolyJet-, SLA-, MJF- en vele andere componenten probleemloos verwerken dankzij aangepaste parameters.
De nadelen van deze technologie zijn dezelfde als die van SRF-technologie. De acquisitiekosten zijn echter zelfs hoger dan die van SRF-technologie, en de afhankelijkheid van verbruiksmaterialen is groter door het gebruik van meerdere consumables.
Wat betreft verbruiksmaterialen moet de huidige selectie (mei 2024) ook als een nadeel worden beschouwd. Tot op heden zijn er slechts een paar verschillende materialen beschikbaar, wat natuurlijk de variëteit aan toepassingen vermindert.
Desondanks is TAF-technologie een absolute drijvende kracht als het gaat om de oppervlakteafwerking van additief vervaardigde metalen componenten. Dankzij het maximale automatiseringsniveau en de mogelijkheid om de meest complexe structuren af te werken, is deze technologie onmisbaar voor bedrijven die de hoogste kwaliteit met minimale inspanning vereisen.
Zoals deze blogpost hopelijk heeft duidelijk gemaakt, zijn de mogelijkheden voor oppervlakteafwerking van metalen componenten meer dan divers - en niet al deze opties zijn hier zelfs genoemd.
Welke oppervlakteafwerkingsoptie het meest geschikt is voor uw eigen productie, hangt sterk af van de toepassingen die het component uiteindelijk moet vervullen.
Ik hoop dat deze blogpost u heeft geholpen om de vele verschillende oppervlakteafwerkingsopties voor metalen componenten beter te sorteren en dat u de juiste optie voor uzelf heeft gevonden.
Bedankt voor uw aandacht - en tot de volgende blogpost!