Despite increasingly realistic flow simulations using CFD (computational fluid dynamics) programs, wind tunnel tests are indispensable in motorsport. The data obtained from these tests is used by motorsport engineers and teams every year to create more aerodynamic and therefore faster vehicles and to put new design ideas through their paces.
However, wind tunnel tests are extremely time-consuming. It can easily take dozens of hours to obtain meaningful flow data. If a large number of designs also have to be tested, it is easy to imagine that wind tunnel tests take more than just hours or days to deliver the best results.
These long test times naturally lead to a high demand for wind tunnel tests. At the same time, however, wind tunnels suitable for motorsport are few and far between. Furthermore, in many areas of motorsport, the times that teams are allowed to use for wind tunnel tests are regulated in order to make the competitive conditions fairer. In Formula 1, for example, the teams will only have between 840 and 1,380 hours in the 2024 season to obtain all the necessary data, depending on their position in the competition in the previous year.
Time is therefore essential for wind tunnel tests. Data must be obtained and processed as quickly as possible and the designs adapted immediately in order to carry out as many wind tunnel tests as possible in the shortest possible time - and this is where additive manufacturing comes into play.
This blog post will focus on the benefits and applications of 3D printing for wind tunnel testing. Find out how this revolutionary manufacturing technology makes wind tunnel testing more efficient, both in terms of time and cost, and why more and more motorsport teams are turning to 3D printing for their wind tunnel testing. At the end you will also find our ideal solution for the 3D printing of wind tunnel model components.
But before we get to that, let's first explain what wind tunnel testing is and why it's so essential to motorsport. If you already know enough about wind tunnels, the button below will take you directly to the benefits of 3D printing for them.
From the 'whirling arm' to advanced technology
The emergence of wind tunnels was closely linked to the development of aviation. The first experiments on the drag and lift of various objects were carried out using the so-called 'whirling arm', which was invented in the early 18th century by British military engineer Benjamin Robins. This technology was later also used by Sir George Cayley, inventor of the first airworthy glider, and the "father of aviation" Otto Lilienthal, who turned the "heavier than air" idea into reality with his gliding experiments, which would revolutionize aviation in the long term.
This 'whirling arm' was of course still a long way from today's wind tunnels, but nevertheless laid an important foundation for their development. The first fully functional and closed wind tunnel was finally developed by Francis Herbert Wenham in 1871. This breakthrough and the subsequent further developments of this first wind tunnel, for example by Konstantin Tsiolkovsky and Osborne Reynolds, were accompanied by a breakthrough in aviation just a few decades later, when the Wright brothers completed the Wright Flyer, the first manned powered airplane, in 1903 with the help of wind tunnel tests.
Following intensive testing by the French engineer Gustave Eiffel, who revolutionized this technology once again between 1909 and 1912, the further development of wind tunnels was primarily related to military aircraft, which were used for the first time in the First World War. During the Second World War and the Cold War, the wind tunnel underwent a variety of evolutions until the first cars were tested in wind tunnels at the beginning of the 1960s.
These wind tunnel tests were actually less concerned with improving aerodynamics by increasing performance than with reducing the energy consumption of motor vehicles. At least for a few years - until the late 1960s, when the Lotus Formula 1 team, then known as Lotus-Cosworth DFV, used wind tunnel tests to improve racing performance.
These wind tunnel tests resulted in the Lotus 49, which introduced some pioneering developments to Formula 1, such as aerodynamic front and rear wings, and won both the constructors' and drivers' championships with the legendary Graham Hill in 1968.
From this moment on, wind tunnel tests were established in motorsport. More and more teams and competitions used them to drive technological progress - and continue to do so today. Although CFD programs have been able to carry out individual experiments digitally for several decades, wind tunnel tests are essential for intensive testing in motorsport. But how exactly does such a wind tunnel test actually work?
The various types of wind tunnel tests
Obviously, a wind tunnel is required to carry out a wind tunnel test. Such a wind tunnel consists of one or more fans that blow or suck the air through a circular channel with the vehicle model in the center.
To enable the most accurate measurements, the air that hits the test object must be as turbulence-free and laminar as possible. Among other things, vertical and horizontal air baffles are used to smooth the air flow generated by the fans, which still has relatively high turbulence due to the sheer volume and speed. The walls must also be as smooth as possible and ideally rounded to avoid turbulence.
Wind tunnels are divided into different categories depending on the air speed - from low-velocity wind tunnels, with air speeds of up to 480 km/h, to hypersonic wind tunnels, where speeds of up to 36,000 km/h can be reached. In motorsport, subsonic wind tunnels are always used, where the air speed does not exceed 990 km/h.
Within these categories, there are two fundamentally different types of wind tunnel tests - full-scale wind tunnel tests, where a full-size model is tested, and small-scale wind tunnel tests, where smaller scale models are used.
The aerodynamic forces acting on the test model through this air can be measured using a variety of instruments, depending on the reason for the wind tunnel test. The most commonly used instruments are balances specially adapted to wind tunnels, such as underfloor balances, which can be used to measure values such as drag and lift force as well as roll, pitch and yaw moment with an accuracy of less than 0.03 %.
Diagnostic instruments for wind tunnel tests are diverse. Very often, large measuring grids near the front and/or rear axle, so-called aero rakes, are used, but are usually combined with other diagnostic methods, e.g. speed probes, pressure transmitters and many others. Engineers use these to measure the air masses surrounding the test object in order to find out how the air moves around or through the model.
Flow visualization instruments are also frequently used. Various methods can be used for this, from smoke and fog to clusters and small filaments on the vehicle model to laser foil and flow-vis paint, a mixture of oil and color pigments.
The PIV process (Particle Image Velocimetry) is one of the most technologically advanced instruments. Here, microscopically small particles are added to the air and the air is illuminated with a pulsating laser beam. With each pulsation, two images are taken within a short distance of each other, the comparison of which provides very precise results on the air flow in diagnostics. Nowadays, two cameras are often used to capture a 3D vector field.
This excerpt shows just some of the many possibilities with which results can be achieved in wind tunnel tests. But why are these results so essential in motorsport?
Aerodynamics is (almost) everything
"Aerodynamics is for people who can't build engines." This quote comes from the legendary Enzo Ferrari after he was asked about the windshield of his Ferrari 250 TR at the 24 Hours of Le Mans. For this endurance race, his quote proved to be true - Ferrari won the race with Olivier Gendebien and Paul Frère, who elicited this quote from him, at the wheel.
Whether Enzo Ferrari would still sign this quote in the same way today is more than questionable. In the decades that followed, especially from the early 1980s onwards, aerodynamics became increasingly important in motorsport and is now one of the decisive factors between victory, midfield and defeat.
And this is why wind tunnel testing is so important in motorsport. It is the ideal method for testing aerodynamics, improving components and validating new design ideas.
The most important factors of good aerodynamics are air resistance, especially in motorsport competitions in which open-wheelers, i.e. vehicles in which the tires are not protected by body parts, are used, and downforce.
Drag is created in every vehicle by the displacement of ambient air and its friction on the vehicle surface. The higher the air resistance, the more energy is required to bring a vehicle up to a certain speed and keep it there. In open-wheel competitions, this drag is amplified by the exposed tires, which cause enormous air turbulence, disrupting the airflow from the rest of the vehicle.
Lower drag allows the vehicle to reach top speed faster and easier. In competitions where one tank of fuel is not enough for the entire duration of a race, this also reduces the frequency of refueling stops.
Downforce describes a downward lift force that increases the vehicle's grip. Downforce is also referred to as 'aerodynamic grip', which, in addition to the mechanical grip, i.e. the mass of the vehicle, presses a vehicle and its tires onto the track.
This phenomenon is caused by the air being split when it hits the vehicle. To generate downforce, parts of the vehicle, such as the front wing, are designed in such a way that the lower air reaches higher speeds and therefore exerts less pressure than the air on the upper side, pushing the vehicle down onto the track.
Downforce is particularly relevant for cornering speeds. The more downforce there is, the faster a vehicle can drive through a corner thanks to increased grip and therefore greater transfer of lateral forces to the track as well as easier handling.
At the same time, however, greater downforce also means greater air resistance. The aim of wind tunnel tests is therefore to achieve an ideal symbiosis of both effects in order to maximize top and cornering speeds.
Wind tunnels are also used for many other aerodynamic aspects. But before we make this blog post any longer, let's talk about the advantages of 3D printing in wind tunnel testing.
Better wind tunnel models with additive manufacturing
The advantages of 3D printing are manifold. For the sake of clarity, I will limit myself here to the three most important advantages. So let's get straight to the first advantage of 3D printing wind tunnel models.
Rapid design iterations
One of the biggest advantages of additive manufacturing is the extraordinary production speed. Due to the often limited time that motorsport competition teams have in the wind tunnel, it is essential to be able to deliver customized designs quickly and reliably.
Not only the production times but also the design times are of great importance. The digital models that 3D printing uses as a basis can be adapted very easily and quickly down to the smallest detail.
Even when it comes to completely new components rather than just adjustments, the speed of 3D printing is impressive. With the fully digital workflow and the high level of automation of 3D printing, motorsport engineers can implement their ideas faster than ever before. This reduces the time from idea to testing, resulting in more design iterations in the same amount of time.
The aforementioned automation also leads to the ability for motorsport teams to fully focus on their ideas and new designs. Instead of having to keep an eye on production for a long time, they can simply let the 3D printer do its job - or even say goodbye to production woes altogether with the help of 3D printing service providers.
The conclusion should be obvious - 3D printing saves motorsport engineers and teams huge amounts of time. However, the use of additive manufacturing for vehicle models not only saves time, but also costs.
Low manufacturing costs
Wind tunnel models and the necessary tools are expensive. Full-scale models in particular can eat a huge hole in the wallets of motorsport teams. Therefore, they are naturally always keen to keep the costs of their test models as low as possible - especially because a large number of them are required.
With 3D printing, they have found the perfect way to achieve this goal. Using additive manufacturing, small-scale models and also components for full-scale models can be produced more cost-effectively than ever before using conventional manufacturing methods.
The low material consumption of 3D printing has an exorbitant influence on these lower costs. While conventional methods produce large amounts of material waste as the components are created subtractively, 3D printing only uses as much material as is actually needed. Only support structures and small amounts of leftover material need to be disposed of during 3D printing - and depending on the 3D printing technology, parts of it can even be recycled.
This material consumption can be reduced even further by using internal structures, which can be produced with ease using 3D printing. For example, non-critical components can simply be printed hollow or with lattice and honeycomb structures to save further material.
By reducing production costs, motorsport teams can invest their funds in other areas of their vehicles to achieve the best possible performance in addition to aerodynamics. Such best possible performance is often linked to complexity - and it is precisely this that 3D printing can also massively improve.
More complex components
Motorsport components are becoming increasingly complex. Be it front and rear wings, fairings, mudguards or spoilers - some of the most complex structures are required to increase the aerodynamic performance of a motorsport vehicle.
Additive manufacturing makes such complexity easier than ever before. What would take weeks with traditional manufacturing methods, 3D printing can do in days, and what would take days with traditional manufacturing methods, 3D printing can do in hours.
For example, the production of a mudguard using the injection molding process takes around two to three weeks. However, we at PartsToGo were able to deliver a complete mudguard to one of our customers in just four days after receiving the digital models - fully reworked and ready for use.
Whether complex internal structures, the finest details or large components - 3D printing allows the complexity of form, hierarchy, material and function to be expanded without the massive amount of time associated with traditional manufacturing methods. For example, inner channels with a thickness of just 1 mm can be produced very easily using 3D printing, whereas conventional production methods would require hours of drilling.
This increased complexity allows a variety of goals to be achieved. Weight reduction, functional diversity and performance are just a few of these. In combination with the high production speeds, these complex components can be tested in the wind tunnel as quickly as possible, which means that the application on the final racing car can also be completed more quickly.
All in all, additive manufacturing offers several advantages for motorsport teams. Many motorsport teams have already recognized these advantages and are taking advantage of them. But what applications is 3D printing for wind tunnel models explicitly suitable for?
Not only the models themselves benefit
3D printing not only enables more cost-effective and complex test models - additive manufacturing also makes the entire wind tunnel testing process more efficient. The possible applications of 3D-printed components for and around wind tunnel models are now explained using the three most important areas of application.
Spare parts
The very high speeds in wind tunnels can of course affect the models. Even minimal damage to a component is enough to render subsequent test data useless.
A rapid response to such damage is therefore essential in order to avoid wasting valuable time in the wind tunnel. Of course, it would be possible to simply keep a large number of spare parts in stock for each individual component - but this is not economical due to the high storage costs and the high storage risk.
3D printing creates an economical solution that allows spare parts to be produced on-demand at the fastest possible speed. As a result, 3D printing reduces both potential storage costs and downtime due to malfunctioning components.
Aids
Of course, tools and other aids are also required for testing vehicle models in the wind tunnel. Whether for assembly, maintenance, repair or the wind tunnel tests themselves - tools are essential for such intensive tests.
Many of these aids require a very high degree of individuality for wind tunnel models, as each model has different characteristics. Instead of producing these individual aids in a costly and time-consuming process using traditional manufacturing methods, many motorsport teams use 3D printing.
This allows specific tools, devices and brackets adapted to the aerodynamic requirements to be produced in the shortest possible time. 3D printing also makes it much easier to adapt these tools, which often occurs when models are modified.
Customized vehicle components
As already mentioned in detail, the vehicle models themselves also benefit massively from 3D printing. I would now like to mention a few specific examples of 3D-printed components for wind tunnel models.
In motorsport and wind tunnel testing, engine pistons, roll bars and pedals are often 3D printed to save weight. Among other things, these can benefit from the complex structures and lightweight materials.
Aerodynamic performance is achieved, for example, by 3D-printed brake duct inlets to optimize the air flow for brake cooling and rear wing flaps to increase lift.
Outside of wind tunnel tests, there are many other applications in motorsport - customized protective clothing in particular, from gloves to helmets, are now often produced using 3D printers.
Conclusion
This blog post should have clearly demonstrated how essential wind tunnel testing is to motorsport and how essential 3D printing is to wind tunnel testing. More and more high-level motorsport teams are recognizing these benefits in various competitions - from Formula 1 with McLaren Racing, for example, who have been working with Stratasys® for several years, to MotoGP, where the Yamaha MotoGP team, for example, is working with Roboze to make their wind tunnel testing more efficient.
In the future, there are sure to be many more teams that will take advantage of 3D printing to achieve their goals. The ever-increasing number of service providers is also helping motorsport teams to achieve customized components without having to purchase a 3D printer themselves.
If you would like to find out how we at PartsToGo are already supporting motorsport teams and which materials and printers we can offer for this purpose, our application page on 3D printing in motorsport is the ideal place to do so.
Thank you for your attention - and see you in the next blog post!
Our ideal solution for wind tunnel tests
Last but not least, I would like to present our ideal solution for wind tunnel model components. There are a variety of materials and printing solutions available to print such components - but nothing beats the Stratasys® Somos® PerFORM in combination with the Neo®800.
The Stratasys® Somos® PerFORM is a ceramic composite material with fantastic stiffness, heat resistance up to 270°C and excellent detail fineness. This material is perfect for body parts of wind tunnel models.
Wind tunnel testing requires precision - and the Neo®800 from Stratasys® is the ideal printer for this with a precision of ± 0.1 mm. In addition, the Neo®800 has a build volume of 384 liters, allowing for large format parts in one piece, and outstanding print speed.
Do you need wind tunnel model components with exactly these properties? Then we at PartsToGo are the ideal people to contact! With our express service and our expertise, both in 3D printing and in the commercial sector, we print your parts cost-effectively, to a high quality and exactly according to your requirements.
Do you already have a digital model and want to have it printed? With our order form, which you can access via the button at the bottom left, it's easier than ever! If you still need advice and validation, we will of course also help you - simply go to our contact form via the bottom right button.
Thank you for your attention - and see you in the next blog post!
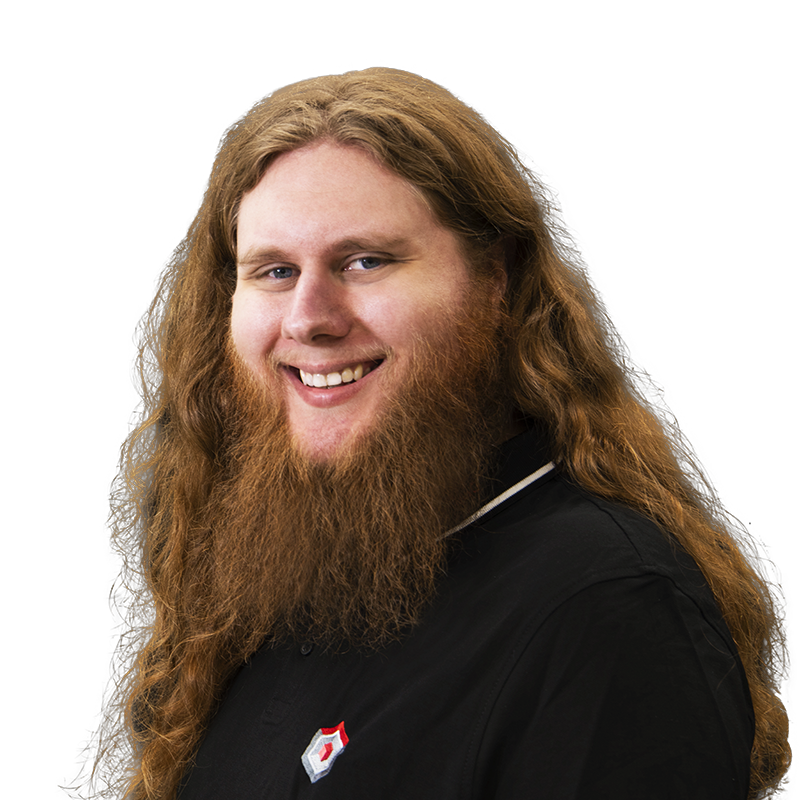